卷绕工艺与叠片工艺有哪些区别?
卷绕工艺与叠片工艺的区别:锂电池制造技术路线解析
一、摘要
本文深入探讨了锂电池制造领域内的两种主要技术路线:卷绕工艺和叠片工艺。文章首先介绍了锂电池在现代电子设备中的核心作用,以及选择合适制造工艺的重要性。随后,分别对卷绕工艺和叠片工艺进行了详细阐述,包括它们的定义、工艺流程、技术特点以及各自的优势和挑战。
在比较分析中,文章着重讨论了两种工艺在结构设计、生产设备、成本效益、技术要求、原材料选择以及性能特点方面的差异。卷绕工艺因其成熟和高效率在大规模生产中占优,而叠片工艺则以其高能量密度和结构稳定性在高端市场中展现出潜力。
文章还探讨了两种工艺在不同应用场景中的适用性,并预测了未来锂电池制造技术的发展趋势。最后,文章总结了选择电池制造工艺时需要考虑的因素,并强调了基于具体需求、成本和技术发展趋势做出决策的重要性。参考文献部分提供了用于撰写本文的相关资源和报告,供读者深入了解。
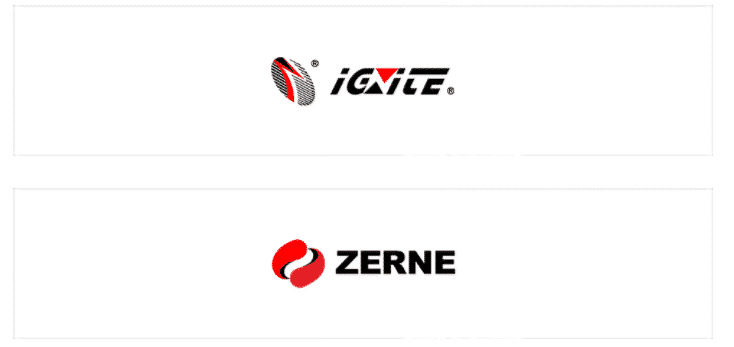
二、卷绕工艺概述
2.1 定义与历史
卷绕工艺是锂电池制造中一种成熟且广泛使用的方法。这种方法的历史可以追溯到1990年代,当时是为了满足日益增长的便携式电子设备需求而开发的。通过卷绕工艺,电池制造商能够大规模生产出成本效益高、性能稳定的锂电池。
2.2 工艺流程详解
卷绕工艺的流程开始于将金属箔材切割成特定尺寸的极片,这些极片随后会被涂上正负极材料。接下来,正极片、隔膜和负极片被顺序放置并通过卷绕机卷绕成紧密的圆柱形或方形结构。这个过程中,极片和隔膜的张力控制非常关键,因为它直接影响到电池的内部结构和最终性能。卷绕完成后,电极卷会被插入到电池外壳中,并注入电解液,然后密封,形成完整的电池。
2.3 技术特点与优势
卷绕工艺的主要优势在于其高生产效率和较低的生产成本。由于工艺成熟,相关的设备和操作技术都非常标准化,容易实现自动化生产。此外,卷绕工艺在提升电池的一致性和可靠性方面也表现出色,这使得它非常适合大规模生产。然而,卷绕工艺也面临着一些挑战,比如卷绕过程中可能产生的“C角”问题,这可能会导致电池内部应力不均,影响电池的性能和寿命。
三、叠片工艺概述
3.1 定义与兴起
叠片工艺是近年来锂电池制造领域的一种创新技术。与传统的卷绕工艺不同,叠片工艺采用层叠的方式将正负极片和隔膜堆叠起来,形成电池的电极体。这种工艺可以提高电池的空间利用率,从而在相同体积下获得更高的能量密度。
3.2 工艺流程特色
叠片工艺的流程涉及将正负极片和隔膜按照特定的顺序和方式交错放置,然后通过压力设备压实,以确保电极结构的稳定性。由于叠片工艺的每个步骤都需要精确控制,因此对设备和操作技术的要求较高。在叠片之后,电池单元会被装入电池外壳,并注入电解液,然后进行密封,完成电池的制造。
3.3 技术优势与挑战
叠片工艺的技术优势主要体现在其高空间利用率和良好的结构稳定性。由于极片是层叠放置的,因此可以更有效地利用电池内部的空间,提高能量密度。此外,叠片工艺还能够减少电池在充放电过程中的内部应力,从而延长电池的循环寿命。然而,叠片工艺也面临着生产效率和成本的挑战。由于工艺较为复杂,目前的生产效率和卷绕工艺相比还有一定差距,且设备成本较高。
四、主要区别分析
4.1 结构设计与性能影响
4.1.1 卷绕工艺的“C角”问题
卷绕工艺中,由于极片被卷绕成圆柱形,会产生所谓的“C角”区域,即极片边缘的弯曲部分。这种结构上的不完美可能导致电池在充放电过程中内部应力分布不均,从而影响电池的性能和寿命。电池制造商需要通过优化卷绕技术和极片设计来最小化“C角”效应。
4.1.2 叠片工艺的层叠优势
叠片工艺由于其层叠结构,可以有效避免“C角”问题。在叠片工艺中,极片以平面形式堆叠,每层之间通过隔膜分隔,从而实现了更为均匀的应力分布。这种结构的优势在于提高了电池的循环稳定性和安全性,尤其是在大容量和高能量密度的应用中表现突出。
4.2 生产设备与操作要求
4.2.1 卷绕机与叠片机的对比
卷绕工艺使用的卷绕机是一种专门设计用于卷绕电极结构的设备。它通过精密的控制极片的送进速度和张力,实现极片的连续卷绕。卷绕机的操作相对简单,但需要精确控制以保证电池的一致性和质量。
相比之下,叠片工艺使用的叠片机则更为复杂。叠片机需要精确地放置每层极片和隔膜,并确保它们对齐准确。这不仅要求设备具有高精度的定位能力,还需要操作人员具备高技术水平,以确保叠片过程的精确性和重复性。
4.2.2 生产效率与设备成本
卷绕工艺由于其成熟的技术和设备,能够实现较高的生产效率,这对于大规模生产来说非常重要。卷绕机的设备成本相对较低,且由于工艺的标准化,维护和运营成本也较为可控。
而叠片工艺,尽管在电池性能上有诸多优势,但其生产效率和设备成本仍然是制约其广泛应用的关键因素。叠片机的设备成本较高,且由于工艺复杂,对操作人员的技术水平要求也更高,这些都增加了生产成本。
4.3 成本效益分析
4.3.1 卷绕工艺的成本优势
卷绕工艺在成本控制方面具有明显优势。由于工艺成熟、设备成本较低,加上可以实现高效率的大规模生产,卷绕工艺在成本效益上非常具有竞争力。这对于价格敏感的消费电子市场来说尤其重要。
4.3.2 叠片工艺的投资与回报
尽管叠片工艺在设备和操作上的初始投资较大,但其在电池性能上的优势,如更高的能量密度和更长的循环寿命,有望在长期运营中带来更好的经济效益。特别是在对电池性能要求较高的应用中,如新能源汽车和高端储能系统,叠片工艺的优势可能会更加明显。
4.4 技术与操作人员要求
4.4.1 卷绕工艺的标准化操作
卷绕工艺由于其标准化的操作流程,对操作人员的技能要求相对不高。操作人员主要负责设备的日常维护和监控生产过程,确保电池的一致性和质量。
4.4.2 叠片工艺的技术挑战
叠片工艺则对操作人员提出了更高的技术要求。操作人员不仅需要精确控制叠片过程中的各种参数,还需要对设备进行精细的调整和维护。此外,叠片工艺的质量控制更为复杂,需要操作人员具备更高的问题诊断和解决能力。
4.5 原材料的选择与应用
4.5.1 原材料的通用性与特殊性
尽管卷绕工艺和叠片工艺在原材料的选择上有很高的通用性,都广泛使用金属箔材作为集流体,以及类似的正负极活性材料和隔膜材料,但叠片工艺对材料的一致性和质量控制提出了更高的要求。
4.5.2 叠片工艺对材料质量的严格要求
叠片工艺中,正负极片和隔膜的尺寸精度、平整度以及抗拉伸性能对电池的整体性能有着直接的影响。因此,叠片工艺要求所使用的原材料具有更高的一致性和质量标准。这不仅增加了材料成本,也对供应链管理提出了更高的要求。
4.6 性能特点与应用前景
4.6.1 叠片工艺的能量密度优势
叠片工艺由于其层叠结构,可以更有效地利用电池内部空间,从而在相同体积下实现更高的能量密度。这使得叠片工艺在需要高能量密度的电池应用中,如新能源汽车和便携式电子设备,具有明显的优势。
4.6.2 卷绕工艺的内阻降低技术
卷绕工艺虽然在内阻方面可能稍高,但通过采用如全极耳或多极耳结构等改进措施,可以显著降低电池的内阻,提升电池的性能。这些结构改进措施有助于提高电池的充放电效率,尤其是在大电流应用中。
五、应用场景与未来趋势
5.1 卷绕工艺由于其成本效益,在大规模应用如消费电子产品中仍占主导地位。而叠片工艺则因其高能量密度和长寿命,在新能源汽车等高端应用中越来越受到青睐。随着技术的不断进步,叠片工艺的效率和成本效益有望得到进一步提升。
5.2 预计未来锂电池制造技术将继续朝着高能量密度、高安全性和低成本的方向发展。叠片工艺由于其在能量密度和安全性方面的潜在优势,可能会在更多应用场景中得到推广。同时,卷绕工艺也将持续进行技术创新,以适应市场的变化和需求。
六、总结
6.1 工艺对比与选择的重要性
本文全面分析了锂电池制造中的卷绕工艺和叠片工艺。卷绕工艺以其成熟的技术、高生产效率和较低成本,在大规模生产中占据优势,尤其适用于消费电子等对成本敏感的市场。相比之下,叠片工艺虽然在生产效率和设备成本上存在挑战,但其提供的结构优势,如更高的空间利用率和能量密度,使其在新能源汽车和高端储能系统中显示出巨大潜力。选择适合的工艺路线对于满足特定应用需求、控制成本和保持技术竞争力至关重要。
6.2 技术优势与应用场景
卷绕电池因其较低的内阻和成熟的生产工艺,在需要快速充放电和成本效益高的应用中表现卓越。而叠片电池则因其高能量密度和优越的循环稳定性,在对电池性能要求更高的领域,如电动汽车和便携式设备中,展现出其独特的价值。
6.3 未来发展趋势
随着技术的不断进步,叠片工艺的自动化水平和生产效率有望进一步提升,成本也有望降低。这可能会使叠片工艺在未来的锂电池市场中占据更大的份额。同时,卷绕工艺也在不断优化,通过结构改进和新材料的应用来提升性能和降低成本。
6.4 综合考量的必要性
电池制造商在选择生产工艺时,需要综合考量电池的应用场景、市场需求、成本预算以及技术发展趋势。同时,还需要关注新兴技术的发展,以便及时调整生产策略,把握市场机遇。
6.5 创新与可持续发展
锂电池技术的持续创新对于推动能源转型和实现可持续发展具有重要意义。随着全球对清洁能源和电动汽车的需求不断增长,锂电池作为核心组件之一,其制造工艺的改进和优化将是支持这一转型的关键因素。